Enhancements in High-Speed WEDM Machines
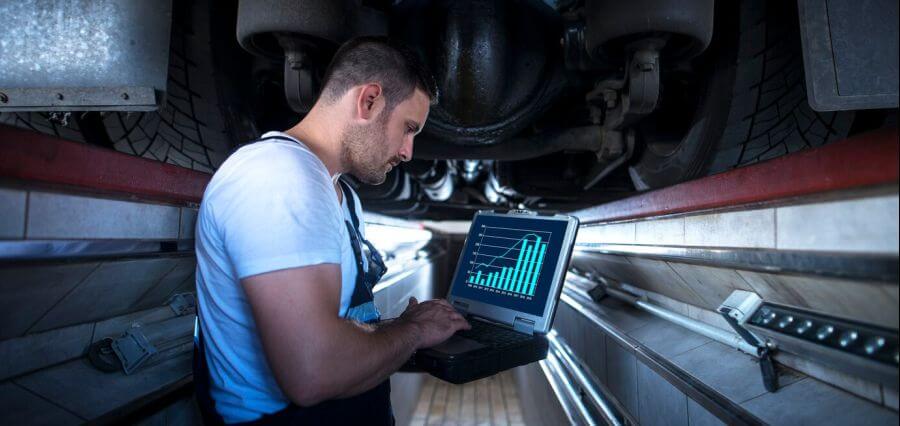
The continuous advancement of technology has led to significant improvements in wire EDM machines, with a focus on enhancing productivity, reducing costs, and achieving automation. The demands placed on wire EDM machines far exceed those of traditional CNC-controlled equipment, necessitating the development of more advanced systems.
One key aspect of enhancing wire EDM machines is the need for precise workpiece management in order to improve product quality and output. By integrating customized CNC machining technology with arc-cutting methods, more flexible and efficient machining solutions are possible, resulting in higher precision and efficiency.
Machine structure and component selection play a vital role in the development of wire EDM machines. Traditional traction methods have limitations such as low machining accuracy, slow cutting speed, and low efficiency. To address these issues, outdated semi-automatic CNC wire-cutting machines should be replaced with customized automatic control systems for high-speed operation. An improved EDM integrated drive device, incorporating a variable frequency motor with additional gears, can provide more tailored solutions for different machining needs.
Improving the electrode assembly in wire EDM machines is crucial for meeting the requirements of CNC wire-cut EDM machines. Special cable devices, rigorous material selection, and optimization solutions like anti-rust coatings and lubricating adhesive sheets can help enhance the efficiency and accuracy of the machining process.
Design and manufacturing improvements for EDM machines involve utilizing corrosion-resistant materials, implementing positioning devices, and protective covers to ensure smooth processing. Proper gap control during installation, managing motor speeds, and addressing power supply issues can help optimize the performance of wire-cut EDM machines.
Enhanced machine debugging and results can be achieved by considering dimensional accuracy requirements, selecting appropriate power supply parameters, and anticipating potential failures to formulate effective solutions. By improving processing technology and implementing technical advancements, wire-cut EDM machines can offer higher efficiency, precision, and cost-effectiveness in machining operations.
In conclusion, the ongoing development of EDM machining technology is driving progress in wire EDM machines, leading to improved capabilities and cost reductions. Embracing advanced EDM methods in future development will not only ensure high product quality and precision but also yield economic benefits by meeting market demands effectively.